Solution to the Problem - Complexities of Decarbonization Technologies in Steel Production
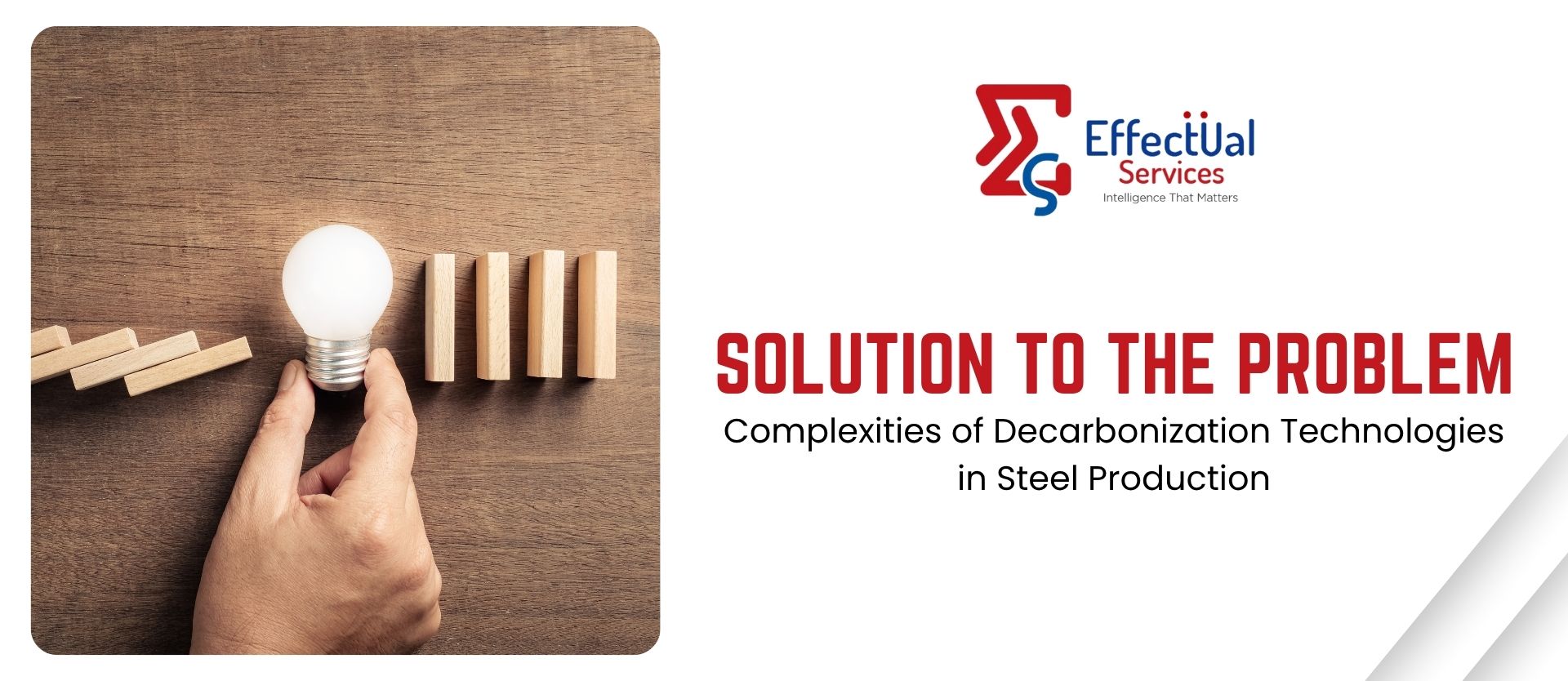
Calix – Zero Emissions Steel Technology (Zesty)
The solution to the problem is proposed by Calix
Summary of the Solution
Technology Provider: Calix
Type of Complexities:
- Lower Hydrogen availability & Higher hydrogen cost
- Need of pellatisation & sintering step
- Increase Cost & CAPEX
Type of Solution: Device & Methodologies
Decarbonization Pathway: Carbon Direct Avoidence
Advantage's of solution:
- Minimum hydrogen use
- Eliminating the need for energy and carbon intensive agglomeration, namely pelletisation or sintering.
- The lowest cost decarbonisation
Raw material for Steel Production: Iron ore
Steel Production Process:
- Reduction
- Electric Heating
Amount of Carbon reduction: Calix's "ZESTY" (Zero Emissions Steel TechnologY)
Complexities in the decarbonisation technology for steel production
- The complete substitution of CH4 with hydrogen in a current DRI iron making process (e.g. MIDREX and HYL) is challenging because the reaction of H2 with iron oxide is endothermic.
- Retrofitting existing blast furnaces to allow partial H2 substitution is also challenging, a certain level of coke is required (>50% of the current coke feed) to maintain the physical structure near the hearth region to distribute gases in the shaft and also ensures that phases are molten in the region below the tuyeres . There are also other substantial issues including material compatibility issues such as H2 embrittlement, high temperature corrosion, increased process complexity and lower thermal efficiency/higher running costs associated with the higher energy requirements
- The utilisation of lower grade ores presents further challenges to shaft furnace based DRI technologies such as Midrex, HYL and Hybrit that rely on pellet and sinter grade where a high crush strength is required to limit fracturing, fines generation and maintain the target productivity. Source
Solution for the complexities
- Indirect electric heating means that hydrogen is consumed as the reductant only (not as the fuel). Calix's ZESTY process is targeting the theoretical minimum hydrogen use (54 kg/t H-DRI for a hematite ore) with a recycle loop to return the unreacted H2 back to the process.
- Capability of processing fines and ultra-fine ore feedstocks thereby eliminating the need for energy and carbon intensive agglomeration, namely pelletisation or sintering.
- Electrical heating and its compatibility with intermittent operation means the process can be heated using renewable energy.
Decarbonisation technology for steel production
The core Calix Flash Calcination (CFC) platform technology: The core Calix Flash Calcination (CFC) platform technology is an in-directly heated, lean-phase calcination technology designed for the flash heating of mineral fines and ultra-fines. In its simplest form, the CFC technology consists of a central process tube which is heated indirectly via an external furnace.
Calix has proven the technology with natural gas and electric heating options . A finely ground mineral (particle size depending on mineral properties and application) is introduced at the top of the process tube, as the mineral falls through the reactor under gravity the particles are rapidly heated predominantly through radiative heat transfer from the walls. Flash heating can be applied to invoke:
- (i) the thermal decomposition of minerals containing trapped or chemically bound volatile components such as carbonates and hydroxides;
- (ii) phase transformations and/or; (iii) facilitate thermochemical gas-solid reactions between the mineral input and an additional reactive gas such as reduction of iron oxide by H2 as is the case for ZESTY. Depending on the application, process gases (including gaseous reaction products) exit the plant via a de-dusting step to remove entrained powder at the top or base of the plant for counterblow and co-flow operation respectively. Calix is scaling the technology through a multi-tube module approach.
Calix's "ZESTY" (Zero Emissions Steel Technology) process
Calix's "ZESTY" (Zero Emissions Steel Technology) process is an extension of Calix's core CFC technology in which
- Iron ore fines iron ore feed (typically < 500 μm) is introduced at the top of the reactor and H2 at the base in a counter-flow arrangement.
- The iron ore is rapidly heated and reduced to a direct reduced iron (DRI) product. The DRI product may be subsequently processed to a Hot Briquetted Iron (HBI) or melted in melting unit to separate gangue from iron for export to steelmakers and/or integration into downstream steelmaking processes (Figure 2-2).
Benefits of the ZESTY Technology
The key benefits of the ZESTY technology that will be demonstrated through the proposed demonstration plant include:
- Compatibility with low grade hematite/goethite ores, consistent with the forecasted decline in quality of Australian iron ore
- Capability of processing fines and ultra-fine ore feedstocks thereby eliminating the need for energy and carbon intensive agglomeration, namely pelletisation or sintering
- Electrical heating and its compatibility with intermittent operation means the process can be heated using renewable energy.
- Indirect electric heating means that hydrogen is consumed as the reductant only (not as the fuel). Calix's ZESTY process is targeting the theoretical minimum hydrogen use (54 kg/t H-DRI for a hematite ore) with a recycle loop to return the unreacted H2 back to the process. Source
Advandanges of the Decarbonisation technology for steel production
ZESTY's key features & benefits
- Electrification & renewable power – The entire ZESTY process can be renewably powered, including the delivery of high temperature heat required to convert iron ore to metallic iron.
- Minimum hydrogen consumption – Calix's unique indirect heating approach ensures that hydrogen is used only as a reductant in the production of green iron and steel. Hydrogen is not combusted or used as a fuel, and unreacted hydrogen is simply recycled.
- Process fines & lower grade ores – ZESTY is ideally suited to process small particle sizes, creating multiple beneficiation opportunities for lower grade ores and fine material that may otherwise be discarded as waste. ZESTY's compatibility with lower grade ores provides a pathway to decarbonise much of the world's current iron ore supply that is otherwise not suitable for use in electric arc furnaces.
- No pelletisation – ZESTY removes the requirement for iron ore fines to be pelletised, eliminating process steps and avoiding significant capital and energy costs.
- No fluidised beds – ZESTY delivers a highly simplified process for the processing of iron ore fines and ultra-fines without fluidised beds.
- Flexible operation – Compatible with intermittent and renewable sources of electricity, ZESTY's electric heating provides a high degree of temperature control with fast start-up and shut down, and highly flexible production rates. As such, it may provide a versatile load balancing service to the energy grid.
- Easily scalable – Calix's modular technology can be simply scaled through duplication, de-risking technology scale up and enabling flexible production volumes.
- Targeting lowest cost – By enabling efficient electric heating, minimal hydrogen use, and eliminating additional processing steps, ZESTY aims to deliver the lowest cost decarbonisation solution for green iron and steel. Source
Decarbonisation technology for steel production
CALIX'S "ZESTY" IRON PROCESS
Calix's "ZESTY" (Zero Emissions Steel TechnologY) Iron process involves the use of Calix's core "kiln" technology to reduce iron ore to iron in a hydrogen atmosphere at between 600oC to 800oC, about 1000oC lower than a conventional blast furnace, due to the ability of Calix's technology to handle small particle sizes in a controlled atmosphere. Calix's kiln can also be easily electrically heated and handle intermittent operation – and thus the process can be energised via renewable energy sources. Because expensive hydrogen is not consumed as a fuel, and only as a reductant, Calix's process is targeting the theoretical minimum hydrogen use of 54 kg per tonne of iron.
In summary, Calix's ZESTY iron technology allows for:
- Reduced temperature of operation
- No pelletisation required – can process fines
- Able to be renewably powered, with intermittent operation
- Can approach theoretical minimum hydrogen use.
CALIX'S "ZESTY" STEEL PROCESS
Calix's "ZESTY" (Zero Emissions Steel TechnologY) Steel process involves the use of the ZESTY Iron process feeding a standard (continuous) electric arc furnace (C-EAF), with the addition of a LEILAC kiln to produce zero-emissions lime. The "hot, active" lime produced from the LEILAC technology can be directly fed to the ZESTY reactor, and in addition any extra CO2 required in the C-EAF for the final steel mix can be fed directly from the LEILAC reactor. Some extra lime from the LEILAC reactor can also be used to scrub any excess carbon dioxide, as well as other pollutants such as sulphur compounds, from the exhaust gas from the C-EAF in a carbonation step ("CL" in the diagram). In addition to the advantages of Calix's ZESTY Iron process, Calix's ZESTY Steel technology allows for:
- use of zero emissions lime in steel-making
- no lime pelletisation / preparation required – can process fines directly
- can also use the lime to scrub any excess carbon, as well as other pollutants, from the exhaust gases. Source
Testing ZESTY's economic and environmental credentials
- To demonstrate the ZESTY technology at a commercially relevant scale, Calix is building a 30,000 tonne per annum ZESTY Demonstration Plant. The FEED study for the plant, completed in February 2024, was part funded by the Australian Renewable Energy Agency (ARENA) and supported by an expanded ore testing program at Calix's pilot scale facility in collaboration with the Australian Heavy Industry Low-carbon Transition Cooperative Research Centre (HILT CRC) and its partners.
- The extensive pilot-scale tests included over 130 test runs using nine different Australian ores from multiple providers, covering a range of grades and particle sizes. The results are extremely encouraging.
- Even at pilot-scale in a multi-purpose R&D plant, ZESTY delivered excellent metallisation rates. Most test runs at the targeted temperature range achieved the level of metallisation suitable for downstream use in either a melter or blast furnace, while several tests reached sufficient metallisation levels for feed directly to an electric arc furnace. Notably, these results are for hematite / goethite ores, representative of around 96% of Australia's iron ore exports. Source
Results & Conclusion
- The ZESTY Demonstration Plant FEED study found that HBI from low grade iron ore could be produced for ~AUD$630-$800 / tonne. This cost includes the capital cost of the plant and processing costs, and excludes the cost of land and transport of the input and output materials.
- The study showed that, even at demonstration scale, ZESTY could produce zero emissions iron at a cost close to the range of existing conventional HBI processing costs, despite using hydrogen as a reductant. Furthermore, it does not take credit for any carbon price, carbon border adjustment mechanism, or other green premium that a near zero emissions iron product may attract.
- The estimated production cost is made possible by a combination of ZESTY's minimal use of hydrogen, the relative simplicity and efficiency of the electrically heated process, and the elimination of the agglomeration and induration process steps.
- ZESTY's energy requirement is projected to be 4.2–4.6MWh / tonne of iron, with most of this energy going towards the generation of green hydrogen. Excluding hydrogen production, ZESTY is projected to require 0.9–1.3MWh / tonne of iron.
Summary:
Calix Limited is an environmental technology company solving urgent global challenges in industrial decarbonisation and sustainability.
Company Information
Calix's patented core platform technology delivers efficient indirect heating of minerals to enable electrification of industries, efficient capture of unavoidable CO2 emissions, and green industrial processing solutions.
Calix is pleased to announce the filing of a patent covering a new application of its core technology for the production of zero CO2 emissions iron and steel.
Calix's ZESTY iron technology allows for:
- Reduced temperature of operation
- No pelletisation required – can process fines
- Able to be renewably powered, with intermittent operation
- Can approach theoretical minimum hydrogen use Source
Australian environmental technology company, Calix Ltd has announced it has been awarded a US$15 million grant from the Australian Government's Carbon Capture Technologies Programme. The grant will support the construction of a world-first renewably powered carbon capture and utilisation (CCU) demonstration plant in South Australia to produce near zero emissions lime and supply captured industrial CO2 emissions to the HyGATE funded Solar Methanol 1 project (SM1)
Highlights
Foundation Year | Industry | Location | No.of Employees | Revenue | Type of organization | Website | Key-People |
---|---|---|---|---|---|---|---|
2005 | Coating chemicals | Pymble, NSW | 51-200 | - | Public | www.calix.global | Phil Hodgson Managing Director & CEO |
CN115198043A- Low-carbon smelting system and method based on coupling of blast furnace-steel furnace process and carbon cycle (TRL-3)
The solution to the problem is proposed by CISDI Engineering Co Ltd CN115198043A Published on 2022
Summary of the Solution
Technology Provider | Type of Complexities | Type of Solution | Decarbonization Pathway | Decarbonization Technology | Advantage's of solution | Raw material for Steel Production | Steel Production Process | Amount of Carbon reduction |
---|---|---|---|---|---|---|---|---|
CISDI Engineering Co Ltd | • Steelmaking gas with low CO concentration in the early stage and the later stage of converting is not fully utilized, so that the waste of resources and energy is caused. | Device & Methodologies | • Smart Carbon Usage | • Burning the steelmaking gas with low CO concentration to obtain heat, and using the heat to remove CO from the steelmaking gas with high CO concentration. • Carbon in the steelmaking gas is recycled |
• Reduce fuel • Improving the utilization efficiency of resources and energy |
- | Smelting | CO is reduced by iron per ton About 256kg/t of emission |
Complexities
- The utilization rate of secondary energy in the steel industry is lower at present, in particular to steelmaking gas generated by a steelmaking furnace. Because of the limitation of the process characteristics of the steel furnace, the concentration of CO in the steelmaking gas in the middle stage of converting is high, and the concentration of CO in the steelmaking gas in the early stage and the later stage of converting is low, while steel enterprises generally only recover the steelmaking gas with high CO concentration in the middle stage of converting, and the steelmaking gas with low CO concentration in the early stage and the later stage of converting is not fully utilized, so that the waste of resources and energy is caused. Source
Solution
- As described above, the present invention is based on a blast furnace-steelmaking furnaceThe low-carbon smelting system and method with the process coupled with carbon circulation at least have the following beneficial effects: burning the steelmaking gas with low CO concentration to obtain heat, and using the heat to remove CO from the steelmaking gas with high CO concentration 2 The rich CO gas is heated, so that the steelmaking gas with different CO concentrations is fully utilized, and the carbon in the steelmaking gas is recycled between the blast furnace and the steelmaking furnace, thereby realizing the carbon recycling of the steel smelting system and achieving the purpose of reducing CO 2 And (4) discharging, and improving the utilization efficiency of resources and energy. Source
Technology for the low-carbon smelting
Low-carbon smelting system and method based on coupling of blast furnace-steel furnace process and carbon cycle
- Coupling system: Low-carbon smelting system based on a coupled carbon cycle of a blast furnace-steel making furnace process, which includes a blast furnace 100, a steel making furnace 200 and CO monitoring device 300.
- Heating Device (500): This device is connected to the steelmaking furnace and is responsible for collecting steelmaking gas with a CO concentration of less than 40%. This gas is then burned to generate heat.
- Heat Utilization: The heat produced by burning the steelmaking gas is used for recycling and supplying heat for the high-CO-concentration steelmaking gas, so that the low-CO-concentration steelmaking gas is fully recycled.
- Gas Collection and Processing device 400 involves dry decarburization process: This method involves treating of high concentration CO gas collected from the blast furnace. The dry decarburization process focuses on removing CO₂ while leaving behind a gas mixture rich in CO.
- Residual CO-Rich Gas Management:
- CCUS System (807): It is connected to the gas collecting and processing device (400). After CO₂ removal, the remaining gas (CO-rich gas) cannot be directly released into the atmosphere due to environmental regulations. Instead, this CO-rich gas is managed through CCUS system.
- Recycling: The CO-rich gas is collected and directed back into the blast furnace gas pipe network (808). This recycling loop helps in utilizing the remaining CO effectively, reducing waste and improving overall efficiency.
- Storage Pressurizing Device 600: Enrich CO₂ from the gas collected by the gas collecting and processing and Direct the CO₂-rich gas back to the steel-making furnace.
Proof of Concept for the low-carbon smelting
Summary Table 8 for conventional blast furnace vs coupled carbon cycle low carbon process
Parameters | Conventional blast furnace-steelmaking furnace process | Coupled carbon cycle low carbon process |
---|---|---|
Coal ratio, kg/thm | 160 | 180 |
Gas reducing ratio of furnace chamber gas | 46% | 51% |
CO 2 Emission reduction of kg/t molten iron | - | 256 |
CO reduction in blast furnace-steelmaking furnace process 2 kg/t | - | 270 |
Coke ratio, kg/thm | 355 | 253 |
Fuel ratio, kg/thm | 515 | 433 |
Direct reduction of carbon by proportion | - | 16% |
Steel-making back-spraying CO 2 kg/t steel | - | 12 |
Results & Conclusion Compared with the conventional blast furnace-steelmaking furnace flow, the method has the following advantages:
- Reduced Fuel Ratio reflects better fuel efficiency and lower carbon emissions.
- Direct Carbon Reduction is a clear indicator of improved environmental performance
- CO Emission Reduction contributes to lowering the overall CO emissions. Source
Results & Conclusion
- Through the calculation of the heat balance and the material balance of the blast furnace, the steelmaking gas after decarburization, denitrification and heating is sprayed back to the blast furnace, the fuel ratio is 433kg/t, wherein the coal ratio is 180kg/t, and the coke ratio is 253kg/t.
- Compared with the conventional blast furnace-steelmaking furnace flow, the method has the advantages:
- Carbon-containing fuel is obviously reduced
- Fuel ratio is reduced by 82kg/t
- Direct carbon reduction ratio is about 16 percent
- CO is reduced by iron per ton 2 About 256kg/t of emission
- CO for back spraying of ton steel 12kg/t, converted into ton iron
- CO can be reduced in a blast furnace-steelmaking furnace flow The emission is about 270kg/t
Low-carbon smelting system and method based on coupling of blast furnace-steel furnace process and carbon cycle
Summary:
CISDI Engineering Co., Ltd. is a state-owned engineering company, supplying consulting, engineering design, EPC contracting, and equipment integration services to steel producers all over the world.
Highlights
Foundation Year | Industry | Location | No.of Employees | Revenue | Type of organization | Website | Key-People |
---|---|---|---|---|---|---|---|
1958 | Mining Company | Chongqing, China | 1,001-5,000 | - | Public | www.cisdigroup.com | Xiao Xuewen (Chairman of the Board of Directors) |
Company Information
With over 50 years of experience, CISDI offers quality services for every aspect of production for projects in the metal industry.
CISDI is in a position to provide overall engineering to large iron & steel complex, and is especially good at consulting, overall plant planning, bulk material storage and handling, large-sized blast furnaces, large-sized converters/EAFs, secondary refining, slab caster, hot strip mill, plate mill/steckel mill, reversible cold strip/plate mill, cold strip mill, long product mill, tube mill, processing line, industrial furnace, automation system integration, industrial water treatment, industrial and civil buildings, gas holder, etc. CISDI is currently providing engineering design, EPC contracting and equipment integration services to many big steel producers in China as well as in Brazil and Japan, etc.
LIBERTY and CISDI to collaborate with the Hungarian Ministry of Economic Development on the decarbonisation of Dunaferr steel works. LIBERTY and CISDI will develop and implement a decarbonisation pathway which will see the Dunaferr plant shift from coal based steelmaking to Electric Arc Furnace technology, and in doing so reduce direct CO2 emissions by approximately 80 percent.
CISDI has received a Letter of Award from Taiyuan Iron & Steel Co., Ltd. (TISCO) by which CISDI is supposed to supply engineering design for overhauling #5 blast furnace of TISCO. CISDI is set to overhaul the furnace to extend its campaign life to 18 years and enhance its efficiency. The goal is to achieve leading performance in China, with reduced consumption, high waste heat recovery, advanced automation, and optimized ironmaking with low silicon content and up to 100% pellet charge.
About Effectual Services
Effectual Services is an award-winning Intellectual Property (IP) management advisory & consulting firm offering IP intelligence to Fortune 500 companies, law firms, research institutes and universities, and venture capital firms/PE firms, globally.
Through research & intelligence we help our clients in taking critical business decisions backed with credible data sources, which in turn helps them achieve their organisational goals, foster innovation and achieve milestones within timelines while optimising costs.
Our Services