Complexities of Decarbonization Technologies in Steel Production Overview
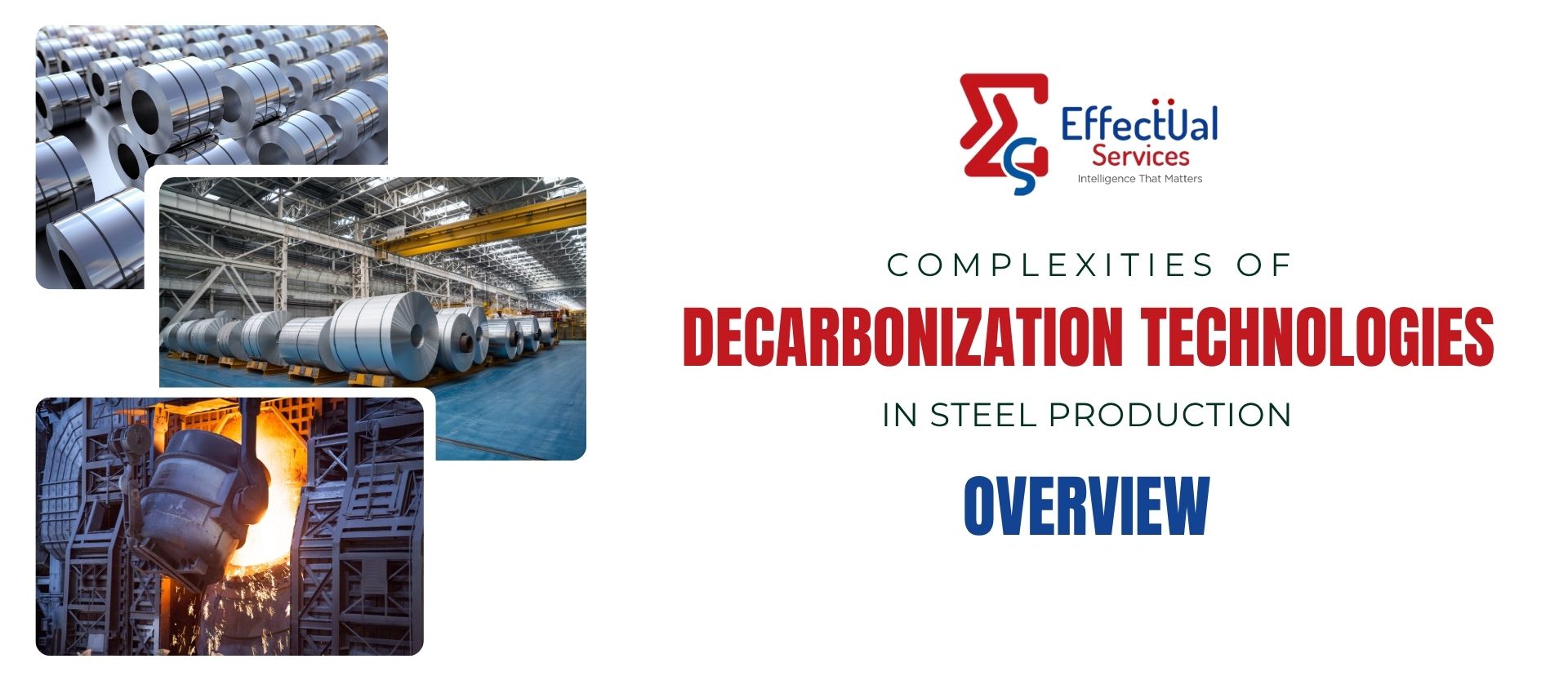
Objective of the Study
The steel industry in Europe is undergoing a significant transformation as it works towards reducing its carbon footprint to zero by 2050, with interim reductions of 30-35% by 2030. This shift involves adopting new production methods, including increased use of scrap and Direct Reduced Iron (DRI) with green hydrogen. These changes introduce new complexities and challenges in industrial production routes. Understanding how similar disruptions have been managed in other contexts can provide valuable insights for navigating this transition effectively.
The study aims to identify and analyze comparable cases of disruption in industrial production complexity and to explore the solutions, methodologies, and strategies that have been successfully employed to overcome these challenges. By evaluating these approaches, the study aims to provide actionable insights and best practices to assist the steel industry in managing its own transition to low-carbon production methods.
Scope of study is worldwide and aims to answer:
- Recommendations on the Complexities of decarbonization technologies in steel production routes.
- Recommendations on successful solutions, methodologies, and strategies used to address the complexities of decarbonization technologies in steel production routes
- Recommendations on proof of concept for the solutions, methodologies, and strategies employed.
- Recommendation on the advantages of solution for the complexities in the decarbonisation technologies in steel production routes. These includes
- Cost effective
- Scalability
- Improve product quality
- Lower production time
- No supply chain issues
- Ease of integration
- Applicable with multiple product
- Others
Complexities in the Decarbonization Technology for Steel Production
- Difficulty in hydrogen availability, storage, and transport
- Hazardous electric arc furnace dust
- Limitation in carbon capture, utilization, and storage
- Low efficiency and scalability of hydrogen-based DRI technology
- High energy requirement
- Increased production time
- High implementation costs
- Difficulty in integration with traditional plants
- Loss of product quality/grades
- Challenges in industrial scalability
Solution for the Complexities in the Decarbonization Technology for Steel Production
- XCarb® Increase
- Energy Availability
- Hybrid Furnace
Background Study (1/5)
The area of study focuses on the complexities that will arise in steel production routes due to decarbonization. Two complexity drivers are central to this issue.
The first driver is the introduction of decarbonized production routes, which will coexist in integrated plants alongside current production routes, sharing some production processes. For example, we will see the coexistence of BF-BOF (blast furnace–basic oxygen furnace) and EAF (electric arc furnace) production routes, both sharing secondary metallurgy processes, casters, and all downstream facilities.
The second driver stems from the fact that the carbon footprint of products will become a specified and committed product property, effectively partitioning current order books by a factor of two or more.
European steel producers have committed to gradually reducing their carbon footprint to zero by 2050, with significant steps of 30–35% reduction by 2030. Initial efforts will focus on increased use of scrap as input material, considered to have a zero carbon footprint. Later efforts will rely on direct reduced iron (DRI), although its carbon footprint is optimal only when the reducing gas used is hydrogen produced with green electricity. The availability of sufficient green electricity in Europe remains uncertain, while large amounts of scrap can be captured from existing export flows. Consequently, almost all European steel producers are investing in EAF production routes.
However, EAF will only partially replace BF-BOF routes, as scrap iron accounts for just 40% of total iron needs. Only the ironmaking and steelmaking equipment will differ between decarbonized and non-decarbonized production routes. Without other motivations to invest in new downstream equipment, new EAF production routes and existing BF-BOF routes will share all downstream production equipment. This effectively doubles the number of production flows, with new points of divergence, convergence, and intersection.
Decarbonisation technology focus
Circular Economy Enhancing the recycling of steel (e.g.scrap in BOF/EAF) and its by products
Smart Carbon Usage Process integration with the reduced use of carbon or internal use of gases
Carbon valorization/carbon capture and usage (e.g. chemical conversion of CO2/CO2)
Carbon direct avoidance Use of renewable energy/electricity (e.g.. Production of H2 replace carbon)
The Circular Economy focuses on minimizing waste through steel recycling and efficient resource use, reducing the need for primary steelmaking and lowering emissions. Smart Carbon Usage optimizes carbon inputs by using carbon capture and low-carbon alternatives like biomass, while also improving energy efficiency. Carbon Direct Avoidance (CDA) aims to eliminate emissions by adopting carbon-free technologies, such as hydrogen-based steelmaking and renewable energy-powered Electric Arc Furnaces (EAF). Together, these pathways provide sustainable solutions to decarbonize steel production, each contributing to a cleaner, more efficient industry.
Background Study (2/5)
Customers are also committed to reducing their carbon footprint, including through the purchase of certified lower-carbon-footprint steel. This has led to various low-carbon-footprint steel offers, based on suppliers' technical capabilities and customer strategies for leveraging carbon footprints. It is unclear whether standardized carbon footprint criteria will emerge for steel, and currently, producers and customers align on different carbon footprint levels on a case-by-case basis, certified in various ways. One emerging principle is that low-carbon-footprint steel should be "physical," meaning suppliers must prove that a particular steel unit has been processed under specific conditions. As a result, steel products specified for particular applications must now be differentiated by their committed carbon footprint, multiplying the number of different products manufactured and creating new complexities in stock management and reallocation of downgraded products.
The complexity of steel production flows, resulting from ArcelorMittal's wide product range, has reached a level that strains manufacturing:
- The scheduling constraints of steelmaking and secondary metallurgy necessitate working in campaigns, which extend the lead time for producing specific steel grades to levels incompatible with customer expectations.
- The number of different campaigns is reflected in the number of transitions, leading to losses: loss of production time, loss of transition slabs between grades, and additional refractory changes, among others.
- The increasing variety of products reduces the opportunities to reallocate downgraded products to alternative first-choice orders.
The current ability to manage these difficulties stems from continuous improvement, which has been relatively successful thanks to the gradual expansion of ArcelorMittal Europe Flat Products' offerings. However, continuous improvement alone cannot address the complexity disruption caused by the sudden integration of Electric Arc Furnace (EAF) production routes in steelmaking plants at integrated sites, nor the sudden doubling or tripling of product variations due to the emergence of low carbon footprint versions of each grade.
ArcelorMittal Europe Flat Products has introduced two low carbon footprint offerings, highlighting challenges with EAF integration into plants: XCarb® Green Steel Certificates: This offering provides steel with a carbon emission reduction certificate, based on process changes like using biologically sourced coal, without adding much manufacturing complexity. XCarb® Recycled and Renewably Produced: Steel produced with a high scrap ratio at the EAF in Sestao, one of the lowest carbon footprint products. Hot rolled coils are either sold directly or finished at integrated sites, where the coexistence of new and regular flows points to increased production complexity.
About Effectual Services
Effectual Services is an award-winning Intellectual Property (IP) management advisory & consulting firm offering IP intelligence to Fortune 500 companies, law firms, research institutes and universities, and venture capital firms/PE firms, globally.
Through research & intelligence we help our clients in taking critical business decisions backed with credible data sources, which in turn helps them achieve their organisational goals, foster innovation and achieve milestones within timelines while optimising costs.
Our Services
Solutions Driving Innovation & Intelligence
Enabling Fortune 500's, R&D Giants, Law firms, Universities, Research institutes & SME's Around The Globe Gather Intelligence That
Protects and Nurtures Innovation Through a Team of 250+ Techno Legal Professionals.