3D Printing in Aerospace Industry
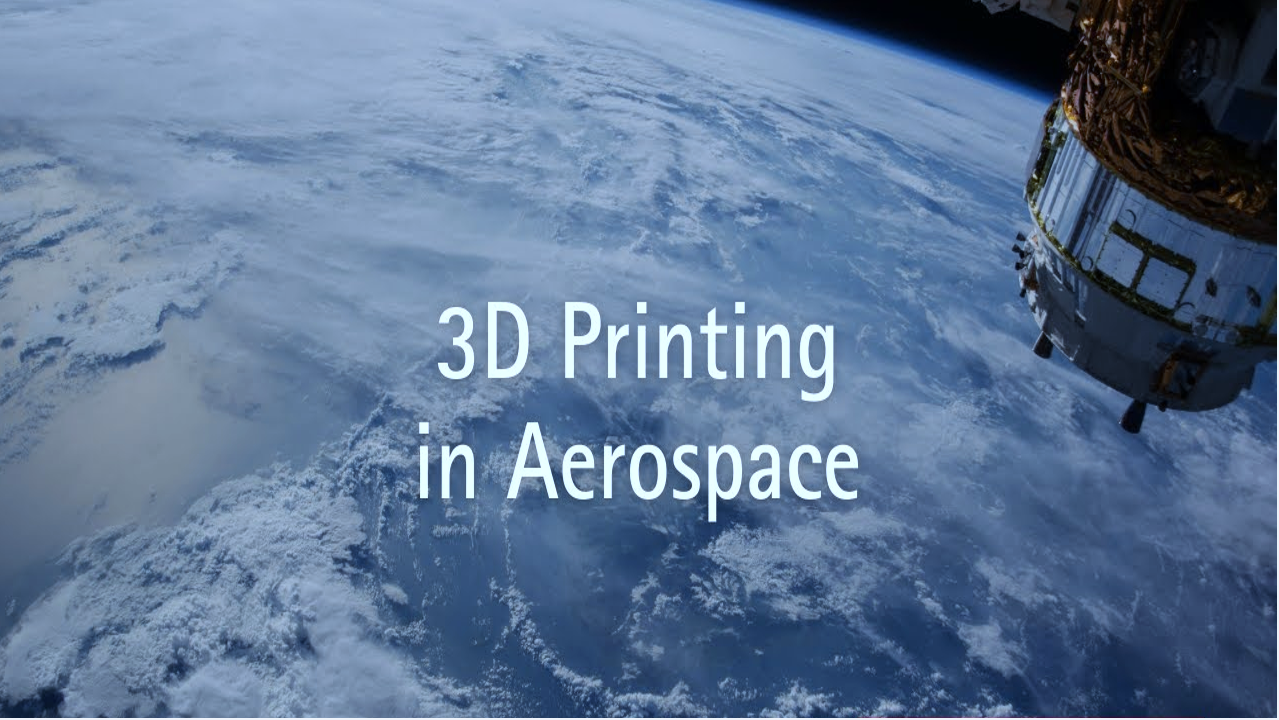
Prelude
Several new technologies are being developed in the current day to make the most convenient and easy use of resources. These days, 3D printing technology has a wide range of applications across several industries because of its simple and rapid usage characteristics. Though it has evolved over the last few decades, the use of 3D printing technology in the aerospace sector has now reached a new height.
There are now numerous uses for 3D printing technologies in the space and aviation industries. In the near future, 3D printing technology will be utilized to manufacture spacecraft and satellite parts in space as well as to construct homes on other planets. At the moment, 3D printers are used in the manufacturing of many parts for spaceships and airplanes. All of the filament materials can be utilized to produce components using 3D printing technology. The primary benefit of 3D printing technology lies in its ability to produce components with varying degrees of complexity at a relatively low cost. These days, the research industry is the main user of this technology because it can print complicated designs of any size, from small to enormous.
In recent years, advances in 3D printing technology have revolutionized the airplane industry. It is more convenient to manufacture small and intricate structures thanks to 3D printing technology. With 3D printing technology, items are built from a geometric computer design by adding materials layer by layer. Every kind of design may now be developed and customized with the help of 3D printing technology. 3D printing technology enables the low-cost manufacturing of components based on user-defined criteria. In contrast to other plastic-forming processes, tooling costs associated with mold development are disregarded. It is feasible to produce highly tailored structures in minimum quantities.
As a result, the aircraft industry may use this technology for many different purposes.
In the aerospace sector, additive manufacturing, or 3D printing, is highly prized. In an industry where reducing weight or drag can result in significant cost savings, 3D printing has made it possible for aerospace makers to produce lighter, more fuel-efficient aircraft at a lower cost.
One of the first sectors to extensively use 3D printing for producing essential components was the aerospace sector, and this technology has completely reshaped the limits of design and production. Aerospace engineers played a key role in the creation of 3D printing, and as the technology advances as a production method, the industry continues to profit.
A wide range of end-use items, including control consoles and nozzles, can be produced using 3D printing in the aerospace industry. This technology can also be utilized to support specific aircraft applications in addition to supporting manufacturing processes. This article will go over the various uses of 3D printing in aerospace, along with the materials and procedures that are employed.
One of the first sectors to use 3D printing was the aerospace industry in 1989. One of the biggest contributors to the advancement of 3D printing technology and procedures since its inception in the 1980s has been the aerospace sector. Even now, the sector continues to be one of the key winners from the process, contributing close to 16% of the industry's overall earnings.
What Was the Origin of 3D Printing in the Aerospace Sector?
In the aerospace sector, 3D printing first appeared in the late 1980s. At the time, the US military and the defense sector benefited the most from 3D printing. These two groups conducted extensive testing and simulation of numerous aircraft systems and components using plastics, which were a less expensive option than metals.
Up until the mid-2000s, the aerospace sector mostly employed 3D printing for testing and prototyping. However, with the development of selective laser sintering and other techniques, flame-retardant resins could also be printed using 3D printing. The first two decades of the twenty-first century saw a growth in the use of 3D printing in aerospace applications. These days, it finds employment across the whole aerospace component lifecycle, from end-use parts in jet engines to tools, jigs for aviation maintenance, interiors of aircraft, and prototyping and verifying designs.
Which Materials Are Used in Aerospace 3D Printing Applications?
Ceramics
Ceramics are non-metallic, inorganic materials. Because of their resilience to corrosion, light weight, and wear, they are excellent for use in aeronautical applications. But ceramics are very fragile and rigid, which makes it challenging to form them into components. Ceramic materials that can be 3D printed into pieces include kaolin and porcelain clay. Satellite mirrors constructed of silicon carbide can be produced via ceramic 3D printing, which aims to improve the stiffness to strength ratio and reduce weight.
Carbon Fiber
Long, incredibly thin, and incredibly strong strands of carbon atoms make up carbon fibers. Because carbon fiber composites are lighter than aluminum and just as robust as steel, they are perfect for use in aircraft applications. This enables the integration of 3D-printed carbon fiber components into the frames and structures of airplanes, improving aircraft performance for manufacturers. However, the aerospace industry's prospective uses for carbon fiber are limited due to its high cost and difficulty of production.
Glass
A molten mixture of silica and other materials is rapidly quenched to create glass, an amorphous material. Glass is a translucent, fragile substance that has been utilized since prehistoric times. Although it is frequently connected to windows, aircraft windows do not employ 3D-printed glass. Alternatively, glass-filled filaments and powders are frequently used to create glass composites, which assist lighten airplanes, and to reinforce plastics.
Metal
In comparison to other materials, metals are ductile, shiny, naturally occurring materials that transfer heat and electricity very well. Because of their excellent strength-to-weight ratios and resistance to corrosion, metals like titanium and aluminum are frequently employed in airplanes. Electrical equipment, frames, buildings, and engine parts are all made of metal that has been 3D printed. The weight of metals is one of their main drawbacks. The performance and fuel efficiency of an airplane might be negatively impacted by having too much metal in it.
Polymers
Materials called polymers are made of molecules arranged in repeating chains. Aerospace uses synthetic thermoplastics like nylon and ABS (acrylonitrile butadiene styrene) as common examples of polymers. Air ducts, seatbacks, wall panels, and other interior components can be 3D printed using these materials. Polymers are generally excellent for use in aircraft applications since they are strong and lightweight. Polymers cannot, however, be utilized in heavy load-bearing applications where metal is frequently favored due to their weakness in comparison to metals.
Inconel
A superalloy based on nickel and chromium, Inconel is prized for its exceptional creep and corrosion resistance as well as its strength at elevated temperatures. Inconel® is frequently used in jet turbine engines to manufacture fuel nozzles for 3D printed aerospace applications. The principal drawback of inconel is its high cost.
Composites
Composite materials are made up of two or more component materials that work well together. The structural advantages of composite materials include high strength, reduced weight, and enhanced wear resistance. The utilization of composite materials in 3D printing technology produces lighter and more structurally robust aircraft by combining the advantageous characteristics of several materials. The fact that 3D-printed composite materials can be costly and non-biocompatible is a drawback.
What Steps Are Included in the Aerospace Industry's 3D Printing Process?
Small-to-medium manufacturing volumes can benefit from the usage of 3D printing, which can also aid in validating part design and performance. These are the components of the 3D printing process that are utilized in the aerospace sector, along with a description of each:
Design
Typically, aerospace designs start out as concept models that highlight specific aircraft parts. Models are made in CAD software and exported to a file format (such as.stl) that is compatible with 3D printers.
Preparation
To guarantee the required print quality, certain preparation work needs to be done before a design can be manufactured by a 3D printer. The preparatory techniques will vary based on the printer being used, the kind of 3D printing, and the geometry of the part. Printer configuration and orientation of part models must be done in a way that guarantees best quality. Additionally, build trays must be heated before to printing in certain printers, such as Fused Deposition Modeling (FDM) and Selective Laser Sintering (SLS) printers.
Printing
Parts can be created once 3D models have been set up as needed and 3D printing systems have been set up appropriately for the kind of 3D printing and printing device being utilized. Print timeframes can range from a few minutes to many hours, contingent upon the component's size and the printing method employed.
Post-Processing
The construction tray can be used to remove parts when 3D printing is finished. Every 3D printed component needs to be post-processed. components printed using one technique can, however, need more post-processing than components printed using a different technique. For instance, DED (direct energy deposition) printed items need additional machining operations to achieve the required dimensions, but FDM produced products frequently simply need the support material to be removed.
Testing
The 3D printed object is tested and assessed when post-processing is finished. If changes to the design are required, 3D printing makes it possible for designers to quickly develop and test new ideas. Once a 3D printed object has served its intended purpose, it can be produced using more conventional techniques or printed again for small-to-medium batch production.
Different Types of 3D Printing Machines Used in the Aerospace Industry
Powder Bed Fusion (PBF) Machines
3D printers known as powder bed fusion (PBF) devices deposit powders and fuse them together using techniques like SLS or EBM. PBF machines have the advantage of recycling wasted powder for use in subsequent printing operations, offering a large selection of metal and plastic materials, and requiring little support to make parts.
PBF machines have several drawbacks, including as sluggish printing speeds, products that are prone to heat deformation, and high power requirements for printing parts.
Fused Deposition Modeling (FDM) Machines
Layer by layer, FDM machines use plastic filament extrusion to construct parts during the 3D printing process. FDM printers have a number of benefits, such as low cost, compact size, and a large range of printable materials. FDM machines do, however, have several drawbacks.
FDM printed parts are weak in directions perpendicular to the print layers and prone to warping. FDM machines also regularly need bed calibration and are prone to nozzle blockage.
Stereolithography (SLA) Machines
SLA machines are 3D printing devices that use a UV lamp to cure photosensitive polymers in order to produce pieces. SLA printers have the capacity to print complicated and complex designs, preserve unused resin for use in future print jobs, and produce parts that are incredibly accurate and precise.
SLA machines do have certain drawbacks, too, like as expensive initial and ongoing maintenance expenses and non-green resins.
Direct Energy Deposition (DED) Machines
A concentrated heat source, such as a laser, plasma arc, or electron beam, is used by direct energy deposition (DED) machines, which are 3D printers, to melt powder or filament.
The main benefits of a DED printer are its ability to manage the grain structure of printed parts and its ability to produce massive pieces with minimal tooling. Parts manufactured with inadequate precision and the requirement for post-processing to achieve required dimensions are drawbacks of DED machines.
Furthermore, DED devices can cost more than $500,000, which might be prohibitive for many businesses.
Binder Jetting (BJ) Machines
PBF (powder bed fusion) machines and binder jetting (BJ) machines are comparable in that the former employ a concentrated heat source to fuse powders together, while the latter deposit liquid binding chemicals onto metal or plastic powders. Large components may be produced using BJ machines, and they also have the advantage of producing parts with minimal or no internal supports and low surface roughness. BJ machines have fragile parts because of their porous architecture and trouble maintaining tolerances and accuracy because of shrinkage. Although adding sintering as a post-process helps strengthen the pieces, it comes with an increased cost.
What Kind of Uses Do 3D-Printed Parts Have in the Aviation Sector?
Engine Components
High mechanical and thermal strains must be tolerated by the materials used to make engine components. Electron beam melting (EBM) and direct energy deposition (DED) are two 3D printing technologies that can be used to create parts like fuel nozzles. Not only are nozzles produced more effectively with these technologies, but the nozzles themselves weigh less than those produced with conventional manufacturing techniques. This has a major positive impact on the environmental impact and aircraft performance.
Structural Components
The external and interior structural parts of an airplane aid in forming and supporting its rigid body. Copper, nickel, and titanium alloys can be used in 3D printing procedures like as EBM and DED to create structural parts like wishbones and brackets.
Maintenance and Repair
Aircraft undergo frequent maintenance and repairs to guarantee their extended lifespan and safe operation. The jigs, fixtures, and tools required for aviation maintenance and repair can be made of titanium, stainless steel, and copper, among other metals, using 3D printing techniques like EBM and DED.
Interior Components
Aircraft interior components range from avionics systems to cabin items like light fixtures and door latches. The popular 3D printing techniques of stereolithography (SLA) and selective laser sintering (SLS) are frequently utilized to produce interior components for aircraft.
Prototyping and Tooling
The processes involved in creating and evaluating new design concepts as well as creating the necessary tools are referred to as prototyping and tooling. Because 3D printing can produce complicated parts on demand with no setup work, it is an excellent solution for producing prototypes and tools for the aircraft sector. This makes it possible to build and test new goods like nozzle bezels and suspension wishbones quickly.
What Are 3D Printed Aerospace Parts?
The mechanical aerospace components listed below can all be produced using 3D printing:
- Fuel nozzles
- Wishbones
- Housings
- Aerofoils
- Door latches
- Lighting fixtures
- Seatback
- Panels
- Trim pieces
Material Jetting 3D printing can create multicolored designs with an injection molding-like surface polish. Before making crucial production decisions, designers can have a better knowledge of the shape and fit of a part thanks to these eye-catching models. Aerodynamic testing and analysis benefit greatly from this extremely accurate prototype process since the surface finish produced by 3D printing is frequently indicative of a final product. Aerospace components that prioritize style above functionality, such door handles, light housings for steering wheels, and entire dashboard designs for the inside, are frequently made utilizing 3D printing.
How does 3D printing improve aerospace manufacturing?
Geometric design freedom
Advanced technical materials and intricate geometries are used in aerospace applications in an effort to reduce weight and increase performance. Interior features, thin walls, complicated curved surfaces, and internal channels for conformal cooling are common features found in aerospace parts.
These properties can be produced using 3D printing, which also makes it possible to create extremely stable, lightweight structures that are exceedingly complicated.
The integration of functional elements into a single component and topological optimization of the parts are made possible by this great degree of design freedom. Additionally, some 3D printing technologies—like binder jetting, SLS, and DMSL/SLM—can produce small batches at affordable prices per unit.
Consolidating assemblies into a single part
The ability to freely create components is another benefit of 3D printing when it comes to combining several elements into one unit.
This lowers the quantity of inventory held at any one time and results in weight savings, which lowers costs.
Surface finish
The aircraft industry places a high value on surface treatments, and 3D-printed items can be post-processed to achieve these surfaces. Certain methods, like Material Jetting, require less post-processing to generate parts that come out of the printer with a smooth, injection-molding-like finish. To increase their precision and surface smoothness, high-performance metal parts made using DMSL/SLM or inexpensive metal parts made with binder jetting can also be polished, smoothed, or even CNC machined after printing.
Part orientation
Part orientation in the build platform is critical for functional pieces that will bear weight. The majority of the parts will have anisotropic mechanical properties and be weaker in the Z direction since 3D printing works layer by layer. This is something that needs to be considered when designing.
Support structures
In 3D printing, support structures are utilized to give a stable foundation for material depositing overhangs or at steeply angled walls (over 45 degrees). Support plays a critical role in metal 3D printing as well, serving to secure the components in the build plate and prevent warping. The regions printed on supports will have some surface markings from the removal of the support and a reduced surface polish. If this is not ideal for your parts, there are procedures like SLS and Binder Jetting that may be done without support structures.
What Benefits Does 3D Printing Technology Offer the Aviation Sector?
Reduced Weight: Lighter plastic components can be substituted for heavier metal ones via 3D printing. The overall weight of the airplane will be decreased by 3D printed components, which will enhance performance and save fuel usage.
Expense-effectiveness: Compared to parts made by conventional manufacturing methods, 3D-printed parts can be made in a significantly shorter number of stages. The procedure is fully automated as well. This lowers waste and overall production costs.
What Drawbacks Do 3D Printing Technologies Have for the Aviation Sector?
Limited Materials: Thousands of alloys and compounds remain incompatible with 3D printing, despite the fact that many commonly used polymers and metals are. This fact restricts the range of possible uses for 3D printing in the aerospace sector.
Weak Part Structure: Parts having anisotropic qualities—that is, properties that vary depending on the direction of an applied load—are produced by certain 3D printing techniques, such as selective laser sintering (SLS) and fused deposition modeling (FDM). This restricts the possible uses of 3D printing for the aerospace industry and may not be acceptable for some load-bearing items.
Who Uses 3D Printing in the Aircraft Industry?
Manufacturers of airplanes, R&D centers, and maintenance companies all employ 3D printing. Rapid aerospace part prototyping, small-to-medium batch manufacture of finished aerospace parts, and the creation of jigs, fixtures, and maintenance equipment for aircraft are all possible with 3D printing.
The aircraft sector continues to benefit from the use of 3D printing. For many years to come, it is anticipated to lessen the aerospace sector's detrimental effects on the environment, support industry innovation, and enhance aircraft performance and production efficiency. Future aerospace uses for 3D printing include green aviation and 3D-printed wings, to name just two.
It is undeniable that 3D printing is changing the production landscape, especially in the highly developed and sophisticated aerospace sector. The two main tenets of this sector are high safety and low weight. By using detailed geometry and complex net shapes that require fewer joints, 3D printing has made it possible to reduce weight. It is still a long way from becoming the accepted standard in terms of safety. Numerous issues, like printing patterns, porosity build-up, uneven print flow, etc., must be fully resolved. All that needs to happen is time. When that occurs, 3D printing will undoubtedly continue to adapt and evolve, eventually replacing a growing number of the conventional manufacturing techniques currently employed in the aerospace sector.
Please feel free to reach out to one of our subject matter experts at info@effectualservices.com
to explore, how we can help you & make the world a better place to live in !!!
Effectual’s 3D PRINTING AEROSPACE RESEARCH FRAMEWORK is a deep dive into this ecosystem and shall help you understand the intricacies of this nascent innovative domain with insights backed with credible data sources. Some ways we can help include, but not limited to - Performing any previous art or freedom to operate searches to help you better grasp the environment surrounding your invention or business endeavours. If certain methods of IP protection are more appropriate for your technological or business goals, we can help you strategize effectively to plan for future & in making continuous innovation a part of your working model.
About Effectual Services
Effectual Services is an award-winning Intellectual Property (IP) management advisory & consulting firm offering IP intelligence to Fortune 500 companies, law firms, research institutes and universities, and venture capital firms/PE firms, globally.
Through research & intelligence we help our clients in taking critical business decisions backed with credible data sources, which in turn helps them achieve their organisational goals, foster innovation and achieve milestones within timelines while optimising costs.
Our Services
Solutions Driving Innovation & Intelligence
Enabling Fortune 500's, R&D Giants, Law firms, Universities, Research institutes & SME's Around The Globe Gather Intelligence That
Protects and Nurtures Innovation Through a Team of 250+ Techno Legal Professionals.