Bio-Polymers in Forming Fabrics for the Paper Industry Overview
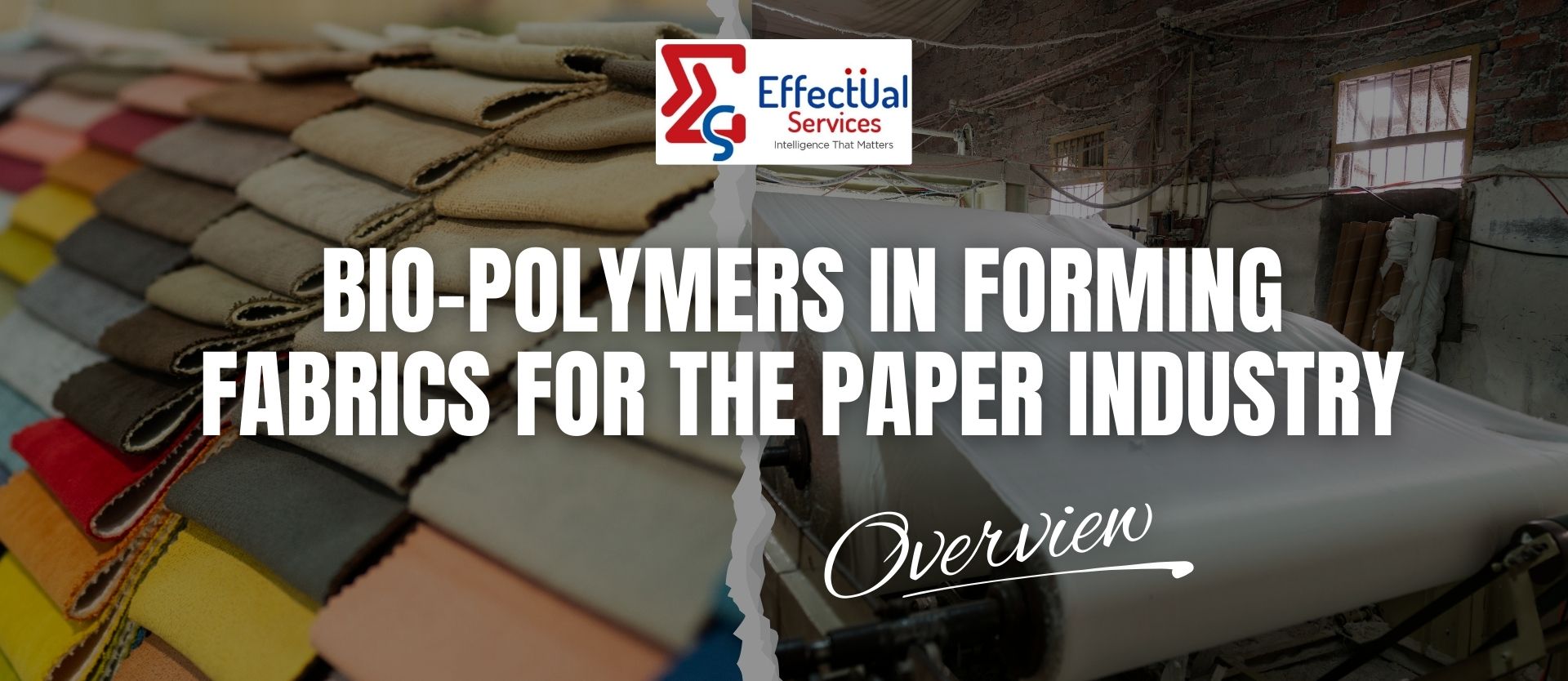
“Forming fabrics" in paper-making endure mechanical stress, abrasion, and chemical exposure while requiring dimensional stability. Monofilaments must resist excessive water absorption in aqueous environments. Current fabrics use polyester (PET) and limited amounts of nylon (PA6) for abrasion resistance, but the material mix complicates recycling. Further, at broader level Paper machine clothing (PMC) refers to the fabrics and felts used in paper machines to support, dewater, and transport paper webs through the forming, pressing, and drying sections, crucial for paper production.
We understand the client wants to conduct to study to explores bio-based monofilaments as a sustainable alternative, aiming to match or exceed conventional performance/cost while enhancing recyclability and reducing reliance on fossil-derived polymers.
The forming fabric, also known as a forming wire, is a woven medium used in the forming section of a paper machine to remove water from the pulp slurry and form a continuous sheet of paper. In the paper making industry, "forming fabrics" play a crucial role in transforming a dilute slurry of paper pulp into a continuous sheet of paper by dewatering and supporting the sheet as it forms, and then carrying it to the next section of the paper machine. "forming fabrics" in paper-making undergo mechanical stress, abrasion, and chemical exposure while maintaining dimensional stability. Monofilaments must resist excessive water absorption. Current fabrics use polyester (PET) and limited nylon (PA6) for abrasion resistance, but this mix complicates recycling. A fully bio-based polymer could enhance sustainability and recyclability. Challenges include durability, chemical stability, and dimensional stability, as excessive water absorption affects performance. Multi-material fabrics also increase recycling complexity and costs. Material innovation is essential for developing bio-based polymers with optimal properties.
We understand that the Client is looking for answers to the below questions:
- What are the bio-based polymers for the preparation of "forming fabrics" which will be used in paper-making industry?
- Recommendation on the proof of concept, test and experimental data information for the physical & chemical properties bio-based polymer.
- Recommendation on the advantages of the bio-based polymers for the preparation of "forming fabrics" which will be used in paper-making industry.
The advantages include:
Recyclable
|
Easily available
|
Stress resistance
|
Cost effective polymer
|
Abrasion resistance
|
Cost effective recycling
|
Chemical resistance
|
Biodegradable
|
Dimensionally stable
|
•Eco friendly
|
Forming fabric for paper making
“Forming fabrics" are critical components in the paper-making process, serving as the initial support for the wet pulp slurry and facilitating water drainage to form a continuous paper sheet. Positioned in the forming section, or "wet end," of a paper machine, these fabrics endure substantial mechanical stress, abrasion, and chemical exposure, necessitating high durability and dimensional stability.
The design and structure of "forming fabrics" significantly influence paper quality and machine efficiency. An optimized fabric ensures efficient dewatering, enhances sheet formation, and contributes to uniform paper properties. Collaborations between paper manufacturers and fabric suppliers are essential to tailor fabric designs that meet specific production requirements. Source
Paper Making Process & Forming Fabric
The papermaking process involves several stages, transforming raw materials (wood pulp, recycled fibers, or non-wood fibers) into finished paper products. The key steps are:
1. Raw Material Preparation: In raw material preparation, wood chips or recycled paper are pulped using chemical, mechanical, or semi-chemical methods. The pulp is then screened and cleaned to remove impurities like bark, dirt, and ink, followed by refining to enhance fiber bonding and improve paper quality.
2. Stock Preparation: The pulp is mixed with additives like fillers, dyes, retention aids, and sizing agents to achieve desired paper characteristics. The mixture is diluted with water to form a slurry (typically 99% water and 1% fiber).
3. Sheet Forming (Wet End Process): The diluted pulp is poured onto a forming fabric (also called a wire) in the Fourdrinier or cylinder machine. The forming fabric act as supporting sheet and allows water drainage while retaining fibers to form a continuous sheet. Suction and gravity help remove excess water as the web moves forward.
4. Pressing: The wet paper sheet passes through large rollers (press felts) to remove more water and improve fiber bonding.
5. Drying: The sheet passes through heated cylinders or air-drying systems to reduce moisture to the final level (typically below 10%).
After treatment, the reeling and finishing process involves winding the finished paper into large rolls or cutting it into sheets. Depending on the end-use application, additional processes like embossing, lamination, or coating may be applied. The image provide the process and steps involved in paper making.
Key Functions of Forming Fabric
Dewatering & Drainage:
- As the pulp slurry is poured onto the forming fabric, it provides a permeable surface that allows water to drain by gravity and suction.
- This dewatering process helps in the initial consolidation of the paper web.
Supporting Sheet:
- The forming fabric acts as a critical support structure in the early stage of paper formation. It is a continuous, porous belt made from synthetic materials (such as polyester) and is responsible for shaping and supporting the wet paper sheet as it forms on the paper machine.
Fiber Retention & Sheet Formation:
The mesh structure of the forming fabric helps retain the fibers while water drains away. It ensures even fiber distribution, affecting the uniformity and quality of the paper sheet.
Control of Paper Quality & Properties:
- The forming fabric influences fiber orientation, which affects paper strength, porosity, and surface smoothness.
- The weave pattern of the forming fabric controls fiber alignment, affecting the strength, porosity, and printability of the final paper.
Control of Paper Quality & Properties:
- The forming fabric influences fiber orientation, which affects paper strength, porosity, and surface smoothness.
- The weave pattern of the forming fabric controls fiber alignment, affecting the strength, porosity, and printability of the final paper.
- It can impact formation defects like flocculation (fiber clumping) and wire marks.
Customization for Paper Grades:
- Different designs (single-layer, double-layer, or triple-layer) allow optimization for various paper grades, from newsprint to specialty papers.
Solutions Driving Innovation & Intelligence
Enabling Fortune 500's, R&D Giants, Law firms, Universities, Research institutes & SME's Around The Globe Gather Intelligence That
Protects and Nurtures Innovation Through a Team of 250+ Techno Legal Professionals.